- 鉭電容器介質(zhì)氧化膜生產(chǎn)方法
- 一步法和二步法生產(chǎn)工藝對比
- 二步法生產(chǎn)聚合物對電容器電性能的影響
- 高含量的氧化劑可以有效增加聚合物的沉積量
- 溫度升高使聚合反應(yīng)速度加快
電子技術(shù)的飛速發(fā)展要求芯片高頻化和電路板高密度組裝,推動了低Res、高容量、耐高紋波電流的電容器發(fā)展。由于MnO2電阻率較低(0.1Ω?cm),所以傳統(tǒng)的MnO2型鉭電解電容器Res大于100mΩ,致使其高頻性能較差。使用新型陰極材料降低電容器的Res是提高鉭電容器高頻性能的重要途徑之一。PEDT導(dǎo)電聚合物熱穩(wěn)定性好、電阻率低,因此在電容器上的應(yīng)用成為目前鉭電解電容器研究領(lǐng)域的熱點。
通常采用電化學法和化學法在介質(zhì)氧化膜表面被覆導(dǎo)電聚合物。采用電化學方法進行聚合物的沉積需要高精度的電極和伺服設(shè)備,而化學聚合法制備聚合物陰極材料對設(shè)備要求較低,因此該方法成為電容器制造商的首選。
使用化學聚合法在鉭氧化物表面被覆聚合物的工藝又可細分為一步法和二步法。其中一步法是浸漬氧化劑和單體預(yù)混合溶液來完成聚合沉積的工藝過程,二步法是先浸漬氧化劑(或單體)后浸漬單體(或氧化劑)來完成聚合物沉積的工藝過程,兩種工藝方法各有優(yōu)劣。
一步法可以嚴格按照理想的化學反應(yīng)計量配制氧化劑和單體預(yù)混合液,這樣可以形成較理想的聚合物鏈,但是氧化劑和單體混合后就開始進行聚合反應(yīng)。隨著混合液中單體和氧化劑含量的提高,聚合反應(yīng)速率加快,盡管用冷卻方法并加入適量的阻聚劑可以降低其聚合反應(yīng)速度,延長混合液的使用時間,但混合液有使用時限,用此法生產(chǎn)成本較高。
二步法在使用過程中由于材料在鉭芯子上吸附量的差異,造成浸漬的氧化劑或單體無法達到理想的化學計量比[r(PEDT:Fe3+)為2.3~2.5],其反應(yīng)生成的聚合物鏈相對較差,由于氧化劑和單體沒有混合,兩者不會發(fā)生反應(yīng),所以溶液不存在使用時限問題,因此可以有效降低生產(chǎn)成本。
筆者重點討論了在用二步法制備聚合物電解質(zhì)的過程中氧化劑含量、聚合溫度等工藝條件對聚合物鉭電容器電容量C、介質(zhì)損耗和Res等電參數(shù)的影響。
1實驗
試樣采用6.3V/150μF規(guī)格的鉭陽極體。選用CV值30k的鉭粉,壓制成尺寸3.3mm×1.4mm×4.3mm,質(zhì)量為140mg的鉭塊,在真空條件下1350℃,燒結(jié)30min,然后將燒結(jié)塊浸于60℃、質(zhì)量分數(shù)為0.1%的磷酸溶液中并對其施加30V直流電壓,在鉭陽極芯體上形成介質(zhì)氧化膜,并使用HP4263B型容量測試儀、38%(體積分數(shù))硫酸測試液測試電容器容量,即C0。然后將已經(jīng)形成Ta2O5介質(zhì)氧化膜的鉭芯子浸入到配置好的氧化劑溶液(對甲基苯磺酸鐵正丁醇溶液)中,取出后在室溫下晾干30min,然后浸漬單體溶液,取出后在室溫下晾干60min,再將其浸在對甲基苯磺酸水溶液中洗去未反應(yīng)的氧化劑、單體及反應(yīng)副產(chǎn)物,重復(fù)此過程8~15次,完成聚合物在鉭陽極塊上的被覆,最后被覆石墨、銀漿,完成聚合物電容器的制備。使用HP4263B型容量測試儀測定樣品容量C、tanδ(120Hz)、Res(100kHz),使用公式:容量引出率=C/C0×100%,計算容量引出率。
2結(jié)果與討論
2.1氧化劑含量對樣品容量的影響
從圖1可以看出,電容器容量引出率隨氧化劑含量的增大而減小。當氧化劑含量達到25%時,容量引出率已經(jīng)降低到一個比較低的水平,約為鉭陽極形成容量的82%。這是因為隨著氧化劑含量的增加,氧化劑很難到達陽極芯子的內(nèi)部,同時有相對較多的氧化劑沉積在鉭芯子微孔內(nèi)氧化膜表面上,氧化劑含量的增加使聚合反應(yīng)速率加快,結(jié)果造成單體溶液還未充分浸入鉭芯內(nèi)微孔就在鉭芯表面附近發(fā)生聚合,形成一層PEDT聚合物層,該層聚合物的存在阻礙了單體溶液的進一步滲透,造成內(nèi)部聚合物沉積少,從而導(dǎo)致電容器的容量減少;而氧化劑含量低時,氧化劑在鉭芯微孔內(nèi)部的沉積數(shù)量相應(yīng)減少,降低了聚合速率,使單體溶液能充分滲入鉭芯內(nèi)部,提高了聚合物在鉭芯內(nèi)部的被覆表面積,從而提高了產(chǎn)品容量。從鉭芯內(nèi)部PEDT的滲入情況剖面圖可以看到,隨著氧化劑含量增大,PEDT被覆到芯子內(nèi)部的量在減小;氧化劑含量減小,PEDT被覆到芯子內(nèi)部的量在增加(見圖2)。
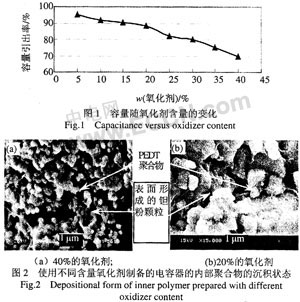
2.2氧化劑含量對聚合物形成的影響
對于二步法生產(chǎn)工藝,單體為聚合反應(yīng)過程中的過量一方,聚合物生成的量由氧化劑的量來決定,聚合物在鉭芯表面的沉積數(shù)量隨氧化劑含量的增加而增加。從圖3可以看出,在相同的浸漬次數(shù)下,使用含量為5%的氧化劑陽極塊的質(zhì)量增加為0.54%,而使用含量為40%的氧化劑陽極塊質(zhì)量增加為3.52%,因此高含量的氧化劑可以有效增加聚合物的沉積量。
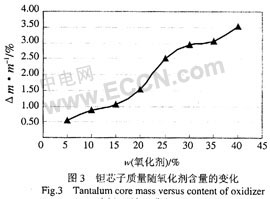
綜上所述,氧化劑含量低,每次浸漬后參加反應(yīng)的氧化劑的量相應(yīng)就少,聚合物的生成量也會相應(yīng)減少,為了形成完整的聚合物陰極層,只有多次浸漬低含量氧化劑溶液,才能形成完整合格的聚合物陰極層,這樣就會造成單體的嚴重浪費和工序時間的延長。而氧化劑含量高,容量引出率低,因此為了避免上述情況的出現(xiàn),在被覆聚合物的過程中需要凋整不同含量的氧化劑。通過實驗,筆者將二步法的工藝過程分為二個工藝段:第一工藝段為鉭芯子內(nèi)部容量引出過程:使用20%的低含量氧化劑溶液引出電容量見圖2(a);第二工藝段為鉭芯子表面聚合物層增厚過程:使用40%的高含量氧化劑溶液增加聚合物陰極層的厚度,見圖4(b)。通過調(diào)整工藝過程達到了減少原材料使用量并縮短工藝時間。
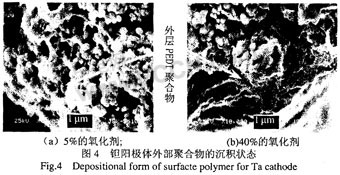
2.3化學聚合溫度對電容器tanδ和Res的影響
聚合反應(yīng)溫度對電容器的tanδ和Res都有較大影響,隨著聚合溫度升高,tanδ和Res有所增大。從圖5、圖6可以看出,當反應(yīng)溫度從25℃增加到50℃后,tanδ由1.88%增加到了3.89%,電容器的Res由35mΩ增加到了56mΩ。這是因為聚合物生成速度與反應(yīng)溫度成正比,溫度升高使聚合反應(yīng)速度加快,溫度每升高10℃,聚合反應(yīng)速率提高一倍,溫度升高使聚合過程中容易生成少量小分子量聚合物副產(chǎn)物,包覆于大分子量聚合產(chǎn)物中形成雜質(zhì),影響聚合物形成完整的網(wǎng)絡(luò)結(jié)構(gòu)。聚合體的機械性能和導(dǎo)電性能依賴于大分子量聚合物形成的交互網(wǎng)狀結(jié)構(gòu),小分子量聚合物的形成,造成聚合物層的導(dǎo)電性能變差,樣品的tanδ和Res增大。
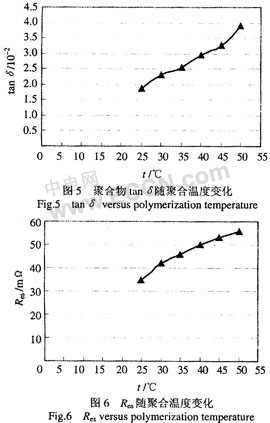
本文討論了影響二步法生產(chǎn)聚合物對鉭電解電容器電性能的影響,并基于試驗結(jié)果得出以下結(jié)論:
(1)在被覆過程中當氧化劑含量超過20%時會影響容量的引出,而使用40%以上的氧化劑能有效增加聚合物的沉積,所以最有效的工藝條件是先采用20%的低含量氧化劑,再使用40%的高含量氧化劑,可以達到最佳的被覆效果。
(2)聚合溫度對電容器的tanδ和Res有較大影響。電容器的tanδ和Res隨反應(yīng)溫度增加而增大,最佳聚合反應(yīng)溫度為25℃。
總而言之,只要采用合適的工藝條件和優(yōu)化工藝流程,使用二步法工藝可以生產(chǎn)出符合要求的聚合物鉭電解電容器,并且可降低生產(chǎn)成本。